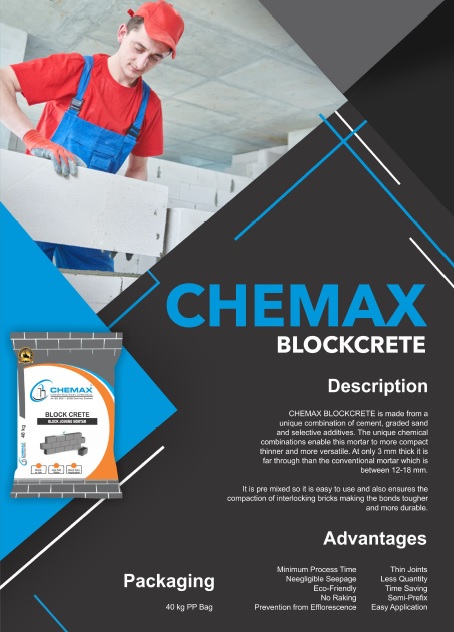
CX CHEMGROUT GP12
It is supplied as a ready to use dry powder. The addition of a controlled amount of clean water produces a free flowing; non-shrink grout for gap thicknesses up to 100mm. CHEMAX GP12 is a blend of Portland cement, graded fillers and chemical additives which impart controlled expansion in the plastic state whilstminimizing water demand
Uses: CHEMAX GP12 is used for precision grouting where it is essential to withstand static and dynamic loads.Typical applications would be the grouting of base plates of turbines, compressors, boiler feed pumps etc., It can also be used for anchoring a wide range of fixings. These include masts, anchor bolts and fence posts.
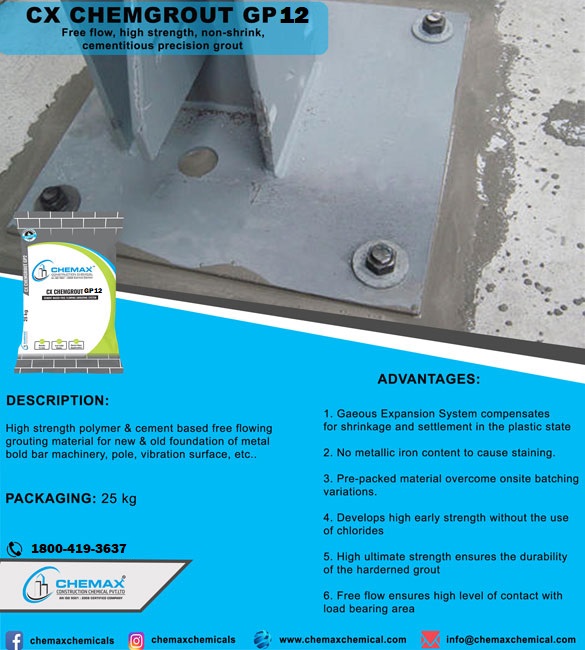
Download Technical Data Sheet

Expansion System
Gaseous expansion system compensates for shrinkage and settlement in the plastic state

Packing
Pre-packed material overcomes onsite batching variations

Process
High ultimate strength ensure the durability of the hardened grout

Ironning
No metallic iron content to cause staining.

Use
Develops high early strength without the use of chlorides

Area Usage
Free flow ensures high level of contact with load bearing area
- Tensile strength (W/P – 0.18) : 3.5N/mm2 @ 28 days
- Pullout bond strength (W/P -0.18) : 17 N/mm2 @ 7 days 20 N/mm2 @ 28 days
- Time for expansion (after mixing) :Start: 20 minutes Finish: 120 minutes
- Fresh wet density : Approximately 2220kg/m3 depending on actual consistency used
- Young's modulus: 28 KN /mm2
- Coefficient of thermal expansion: 11 x 10 -6/0C
- Unrestrained expansion: 2 - 4 % in the plastic state enables to overcome shrinkage.
- Foundation surface : The substrate surface must be free from oil, grease or any loosely adherent material. If theconcrete surface is defective or has laitance, it must be cut back to a sound base. Bolt holes and fixing pockets must be blown clean of any dirt or debris.
- Pre-soaking : Several hours prior to placing, the concrete substrates should be saturated with fresh water. Immediately before grouting takes place any free water should be removed with particular care being taken to blow out all bolt holes and pockets.
- Base plate : It is essential that this is clean and free from oil, grease or scale. Air pressure relief holes should be provided to allow venting of any isolated high spots.
- Formwork : The formwork should be constructed to be leak proof. This can be achieved by using foam rubber strip or mastic sealant beneath the constructed formwork and between joints. In some cases it is practical to use sacrificial semi-dry sand and cement formwork. The formwork should include outlets for pre-soaking
- Unrestrained surface area : This must be kept to a minimum. Generally the gap width between the perimeter formwork and the plate edge should not exceed 150mm on the pouring side and 50mm on the opposite side. It is advisable, where practical, to have no gap at the flank sides.
- Mixing : For best results a mechanically powered grout mixer should be used. When quantities up to 50kg are used, a heavy duty slow speed drill (400-500 rpm) fitted with a paddle is suitable. Larger quantities will require a heavy duty mixer.
- Consistency of grout mix : The quantity of clean water required to be added to a 25kg bag to achieve the desired consistency is given below: Pourable: 4.125 liters Flowable: 4.500 liters The selected water content should be accurately measured into the mixer. The total content of the CHEMAX GP12 bag should be slowly added and continuous mixing should take place for 5 minutes. This will ensure that the grout has a Smooth even consistency.
- Placing: At 300C place the grout within 20 minutes of mixing to gain full benefit of the expansion process. CHEMAX GP12 can be placed in thicknesses up to 100mm in a single pour when used as an underplate grout. For thicker sections it is necessary to fill out CHEMAX GP12 with well graded silt free aggregate to minimize heat buildup. Typically a 10mm aggregate is suitable. 50 - 100% aggregate weight of CHEMAX GP12 can be added. Any bolt pockets must be grouted prior to grouting between the substrate and the base plate. Continuous grout flow is essential. Sufficient grout must be prepared before starting. The time taken to pour a batch must be regulated to the time to prepare the next one.
- Curing: On completion of the grouting operation, exposed areas should be thoroughly cured. This should be done by the use of CX SUPERCURE WB curing membrane, continuous application of water and/or wet hessian.
- Low temperature working : When the air or contact surface temperatures are 100C or below on a falling thermometer, warm water (30 - 400C) is recommended to accelerate strength development. For ambient temperature below 100C the formwork should be kept in place for at least 36 hours. Normal precautions for winter working with cementitious materials should then be adopted.
- High temperature working : At ambient temperatures above 400 C, cool water (below 200C) should be used for mixing the grout prior to placement.
- Health & Safety instructions : CX HARDTOP 330 Special contains Portland cement and is therefore alkaline when in contact with water. Prolonged contact with the skin should be avoided. Any eye contamination should be washed immediately with plenty of clean water and medical advice sought.
- The timing of application CX HARDTOP 330 special is important and critical. If applied too early, bleed or excess water will wash away the cementitious content of the products, thereby making them ineffective. Also denser aggregates sink into the concrete. If the application of CX HARDTOP 330 special is done too late, there will not be sufficient water/moisture to absorb the material into the concrete. Material forcibly applied and trowelled thus, will cause cracks on the surface later, as there is no water/ moisture to hydrate the product.
- Bay edges : CHWhile applying CX HARDTOP 330 special at the edges of the concrete floor or, at the end of bays, extra precaution should be taken by way of sprinkling more material and finishing it smoothly with a steel trowel. This isan additional protection particularly to bay edges where the reaction due to heavy or impact is felt more.
- Curing : ests have shown that proper curing of concrete floors treated with products such as CX HARDTOP 330 special is essential to ensure the physical properties of the floor. The most efficient method of curing by using CB SUPERCURE WB, curing membrane which conforms to ASTM and DOE specifications
- Ready To Use : CX HARDTOP 330 special is supplied ready to use on site. Cement or aggregates should never be added to CX HARDTOP 330 special
- Colored Floors : When a colored floor is required, it is strongly recommended that a job site trial area is laid.
- Surface Treatment : Penetration type surface treatments are recommended to give low porosity and dust proof property.
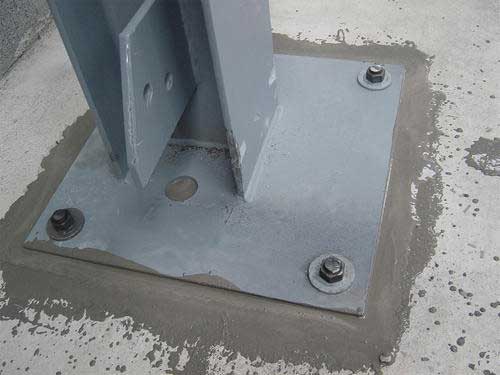